

PPower Team hydraulic pumps, rams, post-tensioning jacks and other equipment offer on-site solutions for demanding construction requirements. That includes new construction and renovation projects for residential and commercial facilities, bridge building and repair jobs, wind turbine construction and maintenance, shipbuilding and more.
Rugged, portable Power Team equipment can handle a variety of applications including post tensioning, pre-stressing, structure jacking, or lifting and positioning. Examples of Power Team equipment commonly used in construction projects include hydraulic pumps, hydraulic rams, inflatable jacks and hydraulic torque wrenches.
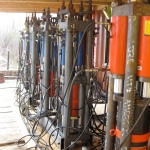
Situation:
Crossing the Mississippi River by ferry has been the only choice north of Baton Rouge, Louisiana since the Civil War. But the ferry was unreliable, slow and a drag on development.The State of Louisiana invested over $400 million to construct a new bridge spanning the Mighty Mississippi to spur economic development and improve transportation in this important industrialized part of the state.
Challenge:
The challenge was to connect St. Francisvillle to New Roads, Louisiana by constructing the longest cable-stayed bridge in North America, with the main span stretching 1583 feet across the Mississippi River. Audubon Bridge Constructors, a joint venture of Flatiron Construction, Granite Construction and Parsons Transportation Group, submitted the winning bid for overall construction.
SPX Power Team was selected to supply lifting jacks, hydraulic pumps and hydraulic hoses for several aspects of bridge construction, including the cofferdams needed to build the original footings for each tower. Richard Dudgeon supplied the hydraulic jacking design and equipment.
Solution:
The design called for two towers rising 520 feet above elevation, with each tower positioned on a pylon constructed on top of 21 eight foot (8′) diameter drilled shafts. Pier footings were built in the Mississippi River but as close to each side as possible to minimize problems with barge traffic in the navigational channel.
Flatiron determined that a cofferdam was needed at each pylon site to withstand a potential high water mark of 80 feet and protect workers as they constructed the footings on the riverbed 40 feet below the top of the river. Conventional sheet pile cofferdams were ruled out as too costly, so a precast concrete cofferdam was used to withstand the river and protect the construction team.
Process:
Modular units were cast on-site in small, manageable sizes for easy transport and erected using a crane. The cofferdam was constructed in sections above the water and then, using hydraulic cylinders and pumps from SPX Power Team, lowered 47 feet in 2 to 4 inch increments into the river. A unique combination of 48 separate 1-3/4″ diameter threaded rods, and Power Team hydraulic jacks sandwiched between steel beams were used to slowly lower these cofferdams into place.
SPX Power Team furnished 200 Ton, 150 Ton, and 55 Ton jacks, along with 10,000 PSI hydraulic pumps. Over 22,000 feet of hydraulic hose was utilized since the hydraulic operation station was located outside of the cofferdam.
Result:
Construction of the cofferdams commenced with the erection of precast panels in November, 2008 and successfully concluded with dewatering upon placement of a final 3,000 yard concrete seal slab in May, 2009. In the Spring of 2011, the ferry was shut down due to dangerously high water levels of the Mississippi River, and the James Audubon Bridge was opened in what the Louisiana Department of Transportation called an emergency opening. The bridge provided uninterrupted access for commuters across the river.
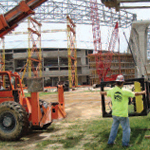
Situation:
A new baseball stadium is under construction on part of the 42-acre Orange Bowl site in Miami. Because Southern Florida weather conditions can vary drastically during the baseball season, the project team designed a facility that would provide fans with a comfortable environment regardless of weather. In addition to 37,000 seats and a natural-grass playing field, the new facility features a retractable roof. Fans will be able to watch baseball in air-conditioned comfort or under the stars, depending on the weather.
Challenge:
The facility’s retractable roof weighs 6,814 tons and is constructed on 12 2,000,000-pound steel trusses that are designed to carry five roof partitions on a rail system 300 feet above the stadium. L.P.R. Construction of Loveland, Colorado, was the steel erector for the operable roof portion of the project. Their responsibilities include building the retractable roof and placing it onto a rail system.
The construction team considered using a crane to lift the trusses into place, but prevailing winds of up to 30 mph in the area posed a safety hazard. Instead, the team chose a unified jacking system to lift each truss four inches and then slide it eight feet into its final position on the rail.
Solution:
L.P.R. researched solution providers with the expertise needed and selected Modern Hydraulics of West Chicago, Illinois. Modern Hydraulics created a special long-stroke four-jack unified jacking system in conjunction with SPX. This system utilizes four 100-ton double-acting Power Team brand cylinders. According to the Modern Hydraulics team, they partnered with SPX for their Power Team brand unified jacking systems for two key reasons:
- They find that SPX equipment, which is manufactured in the USA, provides longer, more reliable service due to superior design and quality. The equipment also delivers stronger, smoother lifting performance, which is critical when lifting 2,000,000-pound trusses 300 feet above the ground.
- They find working with SPX engineering staff to be simple and straightforward, leading to better communications, quicker reaction time and superior results. According to Lance Renshaw, president of Modern Hydraulics, “they listen, react faster and produce a better quality component than their competitors, who rely on off-shore manufacturing.”
Process:
A 2,000,000 -pound pre-loaded steel truss was constructed 300 feet above the stadium floor. The Power Team unified jacking system was used to lift and slide the truss into position on the rail, while maintaining the pre-loaded condition of the truss. It took more than a year to build the steel trusses and move them into position.
Result:
L.P.R. discovered this lifting system worked better than expected and was able to move all 12 steel trusses into place in half the allotted time. As an additional benefit, they can reuse this lifting equipment on other projects across North America because of its high quality and portable, flexible design. The baseball stadium is on schedule to open for the 2012 baseball season.
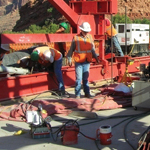
Situation:
U.S. 191 crosses the Colorado River near Moab, Utah, connecting an estimated 1.5 million people a year to the area’s stunning rock formations, trails and national parks. It also serves as part of a major freight corridor that runs from the Four Corners area to Salt Lake City and Denver. The Utah Department of Transportation (UDOT) estimates that a third or more of the traffic comprises semi-trucks and trailers.
Challenge:
Among the goals of the bridge replacement project was to create an aesthetically pleasing structure that would blend into the surrounding landscape. To help achieve this, a segmental bridge design was selected. A major benefit of segmental design is that the precast elements achieve a higher quality of finish and greater strength than cast-in-place box girders.
Segmental bridges also can span greater distances through the combination of post-tensioning and higher compressive strength of the segmental units. This allows for a thinner, more graceful profile with fewer columns.
The layout of the twin bridges, each with spans of 292 feet, 438 feet and 292 feet and only one pier in the water, was also planned to further reduce impacts to the river.
The challenge facing the construction crew was to build these segmental bridges efficiently, economically and with no disruption to existing traffic.
Solution:
The solution involved the use of a unique form traveler system and a little help from SPX.
Engineered to international standards, the form traveler system provides exceptional rigid formwork with a maximum deflection of less than 25 mm at full loading. The system is used to set up forms into which concrete is poured to construct bridge segments one at a time on each side of two large piers. When a counterbalancing segment is finished on each side of the pier, hydraulic equipment moves the form so another segment can be added until the spans meet in the middle between the two piers.
SPX supplied its Power Team® brand high-pressure and low-pressure hydraulic systems to create a complete solution for this movable formwork system.
Process:
Construction crews first built a temporary 400-feet-long bridge from which to work, so as not to disrupt traffic on the existing bridge. They also had to build two large piers to support the concrete bridge.
Using Power Team hydraulic equipment supplied with the form traveler system, the construction crew launched the form traveler on rails to the first segment location. There they aligned and leveled the external formwork and then fixed it into place. Reinforcing steel was placed in the bottom slab and web walls. The interior formwork assembly was then advanced, and the top deck slab soffit and wall forms leveled and fixed into place.
Reinforcing steel and post-tensioning tendons were placed in the deck slab, bottom slab, web wall and deck slab concrete. The post-tensioning tendons were stressed and the internal and external formwork stripped from the cast, cured segment. Power Team equipment was then used again to launch the form traveler to the next segment.
Upon completion of the first bridge structure, traffic was rerouted from the existing bridge to the new two-lane structure. Full four-lane traffic opened with the completion of the second bridge structure.
Result:
The project was completed the end of 2010.
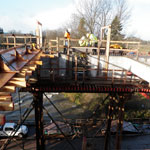
Situation:
Interstate 5 is one of the busiest highways in North America, connecting all major urban centers on the West Coast and Canada to Mexico. In 2002 shear cracks were identified in the forty-year-old Interstate 5 bridges across the Willamette River dividing Eugene and Springfield, Oregon. Temporary bridges were quickly built to keep traffic moving but a more permanent solution was needed. The State of Oregon invested over $200 million to construct a long term, environmentally friendly and aesthetically pleasing solution. SPX Power Team participated in this effort, contributing powerful hydraulic cylinders in an application that demanded power and reliability in a compact package.
General Contractor for the project, Hamilton Construction of Springfield, Oregon, selected Precision Hydraulics LLC of Portland, Oregon, to assist with a key phase in this construction project.
Challenge:
Two arch ribs were constructed to create an arch span. Two arch spans were required to cross the Willamette River and these were cast in place. To replace both the northbound and southbound temporary bridges, nine spans were constructed across the river for a total of eighteen arches. Each arch was constructed on a temporary wooden superstructure, known as falseworks. Once the concrete was poured and cured, two challenges faced the construction team: how to load the ribs safely and how to remove the wooden falseworks. This project required the hydraulic equipment used in this application be load tested and certified to State of Oregon specifications.
Solution:
SPX Power Team provided the muscle, Precision Hydraulics provided the solution, and the University of Washington performed the load testing and certification. Together, SPX Power Team and Precision Hydraulics created a powerful, compact hydraulic ram designed to serve two purposes: lift the concrete arches off of the wooden falseworks while tensioning or “loading” each arch. The hydraulic system, consisting of cylinders, pumps and gauges were assembled, serialized, packed up and delivered by Precision Hydraulics to the University of Washington for load testing and certification.
Each arch consisted of two concrete arch ribs that were designed to meet at the top of the arch. At the very top of each arch a keystone area was left open in between these two concrete sections. A powerful but compact Power Team hydraulic ram was positioned into this vacant space. The heart of this ram was a 965 ton hydraulic cylinder with a 6″ stroke. “Power Team cylinders were the only choice for this application because they combine tremendous lifting power in a small package, and this was a tight space we were working in. They’re rugged and dependable and have proven themselves,” said Precision Hydraulics’ Dave Rogers.
Process:
Standing 60 feet above the roaring Willamette River, the Power Team ram was used to apply pressure to the two arch ribs forming each arch. By pushing against each other, the two halves of the arch lifted up. By carefully coordinating this lifting action, Hamilton Construction was able to lift the entire concrete arch 1-1/2″ to 2″ in 3/8″ increments, enough to clear the falseworks completely. With the lift successful and the concrete arch clear of the wooden falseworks, concrete was poured to fill this “keystone” space, completing each arch. The arch span was properly “loaded” and no longer resting on the falseworks, and the construction crew was able to disassemble and remove the wooden structure.
Result:
All nine spans have been constructed across the Willamette River. The southbound bridge was completed and opened for traffic in the summer of 2011, ahead of schedule. The northbound bridge is currently scheduled for completion in 2013. These two new bridges dividing Springfield and Eugene, Oregon enable Interstate 5 to connect Mexico to Canada and all the major population centers along the West Coast of the United States.
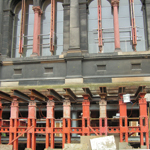
Situation:
Considered a landmark building, a museum in the United Kingdom was undergoing a $67 million renovation to transform the magnificent Victorian building and its facilities into a world-class, 21st century visitor experience for Scotland — and a showcase for international visitors. The project included the creation of 14 new galleries, two hands-on discovery centers, a larger gallery for international touring exhibitions, new facilities for education and a state-of-the-art learning center. A new floor was also to be created beneath the main hall, forming a new street-level entrance, restaurant, shop, cloakroom and visitor reception area.During the renovation project, more than half of the museum property was to stay open to the public.
Challenge:
Among the challenges faced by the contractors and engineers on the project was to lower the basement floor by 4-1/2 feet, removing the basement walls to open up space for the new facilities and street-level entrance. This area runs the length of the main hall, which is situated directly above it. One of the specific tasks involved was to prestress the beams that would hold up the new entrance and inner walls.
Steel beams have various stress values, which determine sheer, bending and other behaviors along their length. Prestressing the steelwork, which creates permanent stresses in the beams, is critical for improving their behavior and strength under various load conditions.
A limited budget ruled out use of a computer-controlled synchronized lift system, requiring the team to seek out alternative methods to safely and successfully prestress the beams.
Solution:
When asked to supply equipment to help in creating the new entrance, a distributor called in the sales manager of SPX’s Power Team® brand, Ian Harris, for assistance.
Mr. Harris, along with the subcontractor, met with the architect and main contractor to discuss how various Power Team brand tools could be used in conjunction with each other to efficiently achieve the same results as a synchronized lift system but in a much more cost-effective way.
The solution devised involved using several Power Team hand pumps and sets of cylinders that would be spread out along each beam. Cylinders were selected that could fit in the very tight gaps available to accommodate the lifting equipment.
Hand pumps were operated a few strokes, and measurements were taken at the stress points along the length of the beam. As each point reached its required stress, the cylinders were locked off.
The process was repeated until all points had achieved the required stress. Each lift took one to two days.
The PowerTeam lifting equipment specified for the task included the following:
5 P300
15 RLS200
5 9765E
5 9635
20 9682
hand pumps
cylinders
hoses
manifolds
fittings
15 9670
15 9575
25 9798
15 9764E
15
tee adapters
shut off valves
couplers
hoses
pressure gauges
Result:
Installation of the beams to support the inner walls and new street-level entrances is complete. The museum reports that the renovation project ran on time and budget.
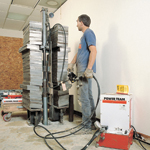
Quiet Hydraulics Help Keep Class in Session
A university business administration building built in the mid-1970s had some structural problems. Back-fill had allowed a 2000 square-foot section of the slab to sink enough so that interior partition doors cracked, walls buckled and ceilings twisted.
The contractor used weighted Power Team® brand C256C hydraulic rams, driven by Power Team brand PQ603 pumps, to drive steel piers through the sinking back-fill and into the weathered shale subsurface below.
They then jacked the slab in stages, using 25 Power Team C256C, 25-ton hydraulic rams in groups of five in a « leap-frog » pattern. Each group used a Power Team P159 two-speed hand pump. The pumps were equipped with 9635 manifold blocks, 9575 valves and 9052 gauges to control the lift.
Permanent steel plates under the slab secured it to the piers. A cement and sand grout was pumped into the void. They then patched the 50 jack holes in the floor, leaving little evidence of the repairs. The quiet operation of the Power Team equipment minimized the disruption of classes in nearby rooms during the project.